In-Depth Analysis of Supply Chain Inventory Models
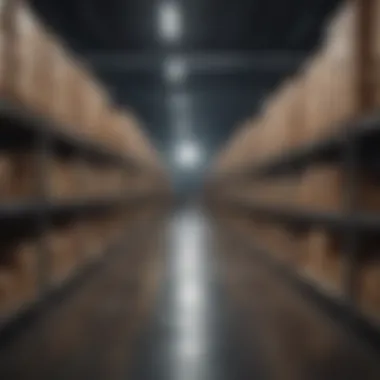
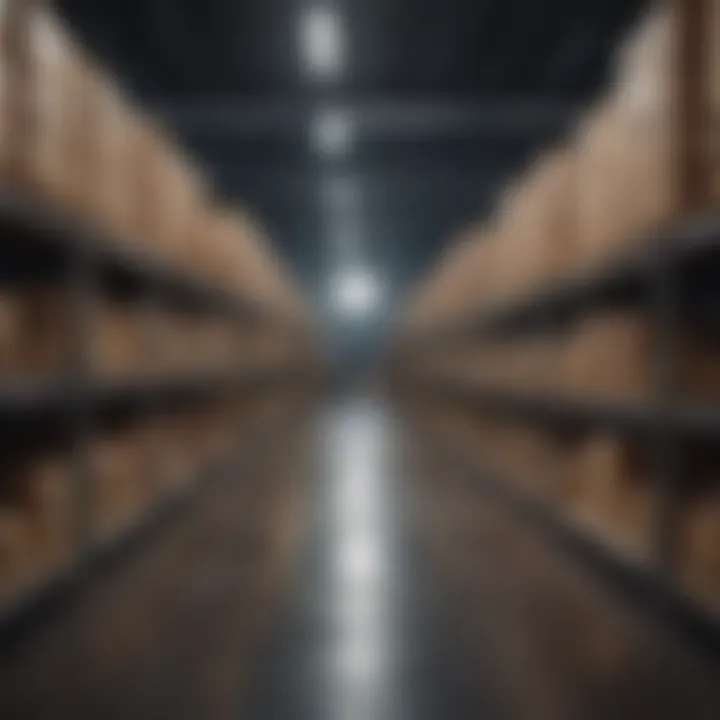
Intro
In the realm of modern commerce, the importance of efficient inventory management cannot be overstated. Businesses today grapple with complexities that can turn inventory into a double-edged sword: while it represents an essential asset, mismanagement can lead to crippling overhead costs and wasted resources. Understanding various inventory models is vital for any organization looking to excel in today’s cutthroat market.
This article aims to unravel the core principles behind several prominent inventory management methodologies, such as Just-In-Time and Economic Order Quantity. As we dive deeper, we’ll explore how demand forecasting, inventory optimization, and innovative technological advancements shape the landscape of supply chain management. Our objective is to provide valuable insights, whether you're just starting out in the field or you're a seasoned professional seeking to refine your strategies.
Key Terms and Definitions
When venturing into inventory management, grasping essential terminology is crucial for clear communication and decision-making. Understanding these terms offers transparency into the methodologies we’ll discuss, and it also enriches the discourse surrounding supply chain efficiency.
Investment Terminology
- Just-In-Time (JIT): This approach revolves around keeping inventory levels low and receiving goods just as they’re needed for production. This method reduces holding costs but demands accurate forecasting.
- Economic Order Quantity (EOQ): EOQ is a formula used to determine the optimal order quantity a company should purchase to minimize total inventory costs. It balances order costs and holding costs effectively.
- Stochastic Inventory Models: These models incorporate randomness in demand and supply, providing a statistical basis for managing fluctuating inventory levels.
Detailed Explanations
Each of these terms relates directly to the strategies that can bear significant weight on a company’s bottom line. Pinpointing the right model to utilize could mean the difference between thriving in the competitive market and barely keeping your heads above water.
Expert Insights
Investment Strategies
To navigate the murky waters of inventory management, it's vital to employ sound strategies grounded in the principles of the aforementioned models. Here are a few insights worth noting:
- Leveraging Technology: Implementing software that integrates supply chain functions can dramatically enhance your forecasting accuracy and inventory optimization.
- Continuous Improvement: Regularly revisiting and analyzing your inventory management systems can help root out inefficiencies. Adopting a kaizen mindset could bolster productivity.
Market Trends Analysis
- Rising Reliance on Data Analytics: As businesses become more technologically inclined, the utilization of data analytics is reshaping supply chain strategies. Companies are now better equipped to predict demand fluctuations and manage inventory stock.
- Focus on Sustainability: A growing trend among firms is the emphasis on sustainable practices, particularly in inventory management. Businesses look to minimize waste and energy use throughout the supply chain.
"An optimized supply chain inventory is not just a competitive advantage—it's a necessity for survival in today’s fast-paced market."
Understanding these insights can position entities to not only thrive but also adapt to the shifting business landscape. With knowledge comes power; thus, harnessing the right inventory models can yield lucrative outcomes.
Prelims to Supply Chain Inventory Models
In today’s fast-paced commercial arena, efficient inventory management may be the whittle that determines the difference between thriving companies and those that merely survive. Supply chain inventory models serve as the backbone of many businesses, functioning as a set of guiding principles that help manage resources effectively. These models provide frameworks for understanding how inventory can be optimized to reduce dangers while enhancing productivity.
When talking about custodied resources, these models offer guidance about what to stock, how much to stock, and when to stock. With a strong grasp of these elements, professionals can make decisions that align closely with customer demand and regulatory requirements, thus flipping the script on operational efficiency.
Further, by maintaining an agile inventory, companies can respond rapidly to market changes. This adaptability not only minimizes holding costs but also ensures that stockouts are kept to an absolute minimum—an essential element in maintaining customer satisfaction.
"The art of stocking inventory is not only about keeping materials on hand; it’s about timing and rhythm, just like a well-tuned orchestra."
Definition and Importance
Supply chain inventory models represent a crucial combination of techniques and processes employed by firms to manage stocks. The crux of inventory management lies in maintaining a balance between supply and demand, avoiding excess stock or shortages. With the right inventory model in place, companies can greatly enhance operational precision, reduce costs, and boost their ability to respond to customer needs.
The importance of these models cannot be overstated. For businesses looking to cut down waste and maximize their bottom line, understanding various inventory types and costs is paramount. In calculating how to stock efficiently, utilizing models clarifies how different approaches, like Just-In-Time or Economic Order Quantity, can be employed to meet specific business objectives.
Historical Context
To appreciate the significance of supply chain inventory models in contemporary management, it’s helpful to take a brief stroll down memory lane. Long before sophisticated software and analytical tools surged onto the scene, inventory management followed more intuitive and less scientific means. Companies either procured materials based on gut instincts or traditional ordering methods, thus necessitating a reimagination of how inventory could be managed.
The advent of mass production in the early to mid-20th century crafted a high-stakes environment requiring businesses to adopt more systematic models. This period saw giants like Toyota lay the groundwork for Just-In-Time production methods, demonstrating how lean inventory practices could streamline operations without sacrificing quality. Over the years, as technology evolved, these early frameworks were integrated with data analytics and business intelligence tools—changing the landscape of inventory management forever.
In light of this history, present-day inventory models are informed not only by economic factors but also experience gleaned from decades of trial and error. Following these templates enables organizations to derive benefits from accumulated wisdom, helping to inform their strategies today and into the future.
Key Components of Inventory Management
Inventory management is the backbone of any supply chain, serving as the thread that weaves together various elements into a cohesive operation. It’s not just about counting the stock on hand; it involves a meticulous balancing act between various components that dictate how effectively an organization can meet the demands of its customers while managing costs. A strong grip on these components allows businesses to streamline processes and adapt flexibly to market changes.
Inventory Types
Inventory can be broadly categorized into three essential types: raw materials, work-in-progress, and finished goods. Each type plays a unique role in inventory management and contributes to the overall efficiency of the supply chain.
Raw Materials
Raw materials are the foundational elements used in the production of goods. These are essentially the ingredients before they are transformed into a finished product. The key characteristic of raw materials is their potential to be repurposed for various products, making them a versatile option for manufacturers. Having a solid inventory of raw materials is crucial because it ensures that production lines can run smoothly without delays.
Unique Feature: One unique aspect of raw materials is their fluctuating prices due to supply chain disruptions or seasonal changes. This can lead to advantages, such as bulk purchase discounts, or disadvantages, like holding excessive stock if demand predictions fall short.
Work-in-Progress
Work-in-progress (WIP) inventory includes all items that are currently being manufactured but are not yet complete. This type serves as an indicator of production efficiency and capacity utilization. Its significance lies in its ability to highlight areas within manufacturing that might be bottlenecks, thus enabling stakeholders to make adjustments.
Unique Feature: The unique feature of WIP is that it remains in flux throughout the production cycle. This continuous transition can either be an advantage when optimizing production schedules or a disadvantage when items are held too long, tying up capital and resources.
Finished Goods
Finished goods are the end products ready for sale or distribution. They represent the culmination of production efforts and directly link to customer satisfaction. The primary characteristic of finished goods is their immediate saleability, which greatly impacts revenue streams.
Unique Feature: The distinct feature here is the dependence on market demand. If demand is overestimated, a backlog can occur, leading to excess inventory and subsequent carrying costs. Conversely, underestimating demand can lead to stockouts, resulting in lost sales and unhappy customers.
Inventory Costs
The costs associated with inventory management are another focal point. They can generally be divided into three categories: holding costs, ordering costs, and stockout costs. Each introduces its challenges and considerations for organizations.
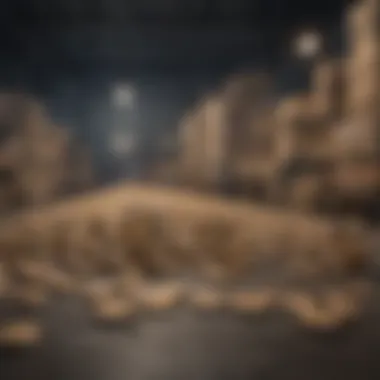
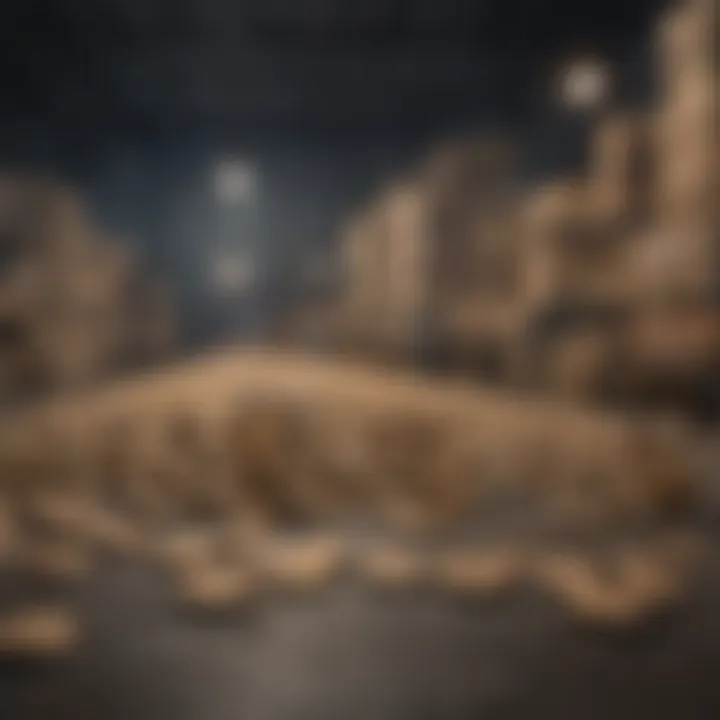
Holding Costs
Holding costs reflect the expenses incurred for storing unsold inventory. These include rent, utilities, insurance, and even depreciation. The key characteristic of holding costs lies in their direct impact on a company's profit margins; the higher the costs, the greater the pressure on pricing strategies.
Unique Feature: One unique aspect is the trade-off between holding enough inventory to meet customer demand and minimizing these costs. Holding excess inventory can lead to wasted resources, while too little can mean missed opportunities in sales.
Ordering Costs
Ordering costs are incurred each time an order is placed for additional inventory. This can encompass delivery charges, processing fees, and labor hours involved in managing orders. The important aspect of ordering costs is their scale—it typically incurs a high initial setup but balances out with larger purchases over time.
Unique Feature: A fascinating feature here is the frequency of the orders. Frequent small orders can lead to higher ordering costs, whereas larger, less frequent orders can help mitigate these costs but require proper demand forecasting to avoid excess stock.
Stockout Costs
Stockout costs arise when an item is out of stock, leading to missed sales opportunities and potential damage to brand reputation. An important characteristic of these costs is their unpredictability—they can vary dramatically based on consumer trends and other external factors.
Unique Feature: The major disadvantage of stockout costs is that they can have a ripple effect throughout the supply chain, causing delays and frustration not just for businesses but also for customers, which can lead to long-term loyalty issues.
"A comprehensive understanding of inventory types and associated costs provides a robust framework for managing stock efficiently, ultimately enhancing organizational performance."
Fundamental Inventory Models
In supply chain management, understanding Fundamental Inventory Models is essential for optimizing inventory practices. These models provide a structured framework for making decisions around ordering, stocking, and managing inventory levels, and they are crucial to aligning inventory management with overall business goals.
Crafting inventory strategies without robust models can lead to untold issues—overstocking leads to increased holding costs while understocking results in missed opportunities or customer dissatisfaction. Fundamental models help navigate these challenges by employing mathematical and analytical techniques, ultimately fostering improved accuracy in forecasting demand and inventory planning.
Just-In-Time (JIT)
Just-In-Time (JIT) inventory management is a well-known approach that's practically synonymous with lean manufacturing. This model revolves around the principle of having the right items available at the right time, significantly reducing wastage. By coordinating closely with suppliers, companies employing JIT often receive materials just as they are needed in the production process.
A hallmark of the JIT approach is minimizing inventory levels. This can drastically cut down on holding costs, and ultimately, free up cash flow for other operational needs.
However, the JIT model doesn't come without risks. Any disruption in the supply chain can jeopardize production schedules, leading to delays and potential loss of customer trust. Moreover, it requires exceptional coordination and communication with suppliers, a commitment that not all organizations can sustain.
Economic Order Quantity (EOQ)
The Economic Order Quantity (EOQ) model is fundamentally a mathematical approach to determining the optimal order quantity that a company should purchase to minimize total inventory costs. These costs include ordering costs and holding costs, which can easily grow unwieldy if not kept in check.
By analyzing these costs, businesses can pinpoint the exact order size that reduces overall expenses. The formula for EOQ is pretty straightforward:
Where:
- D = Demand for the product
- S = Ordering cost per order
- H = Holding cost per unit per year
Though optimal for many environments, EOQ assumes constant demand and lead times, which may not hold true in volatile markets. Despite this limitation, companies often find that adopting EOQ leads to better budgeting and improved inventory predictability.
ABC Analysis
ABC Analysis provides a categorization method of inventory based on its value and importance. By segmenting inventory into three categories—A, B, and C—companies can prioritize management efforts accordingly:
- A items: High value, low frequency of sale (e.g., luxury goods, critical components)
- B items: Moderate value and moderate frequency of sale
- C items: Low value, high frequency of sale (e.g., office supplies, basic components)
This approach allows businesses to apply different management strategies to each category, ensuring that high-priority items receive more attention and resources.
"Effective inventory management requires not just having the right stock available, but also knowing how to prioritize that stock effectively."
While ABC Analysis provides valuable insights, it’s essential for organizations to regularly review these classifications, given that item importance can evolve based on market changes and business strategies.
Understanding these Fundamental Inventory Models sets the stage for grasping more advanced strategies in inventory management, ensuring that companies can adapt their approaches to meet customer demands and operational efficiencies.
Advanced Inventory Models
In the world of supply chain management, Advanced Inventory Models represent a sophisticated approach to optimizing stock levels, maximizing efficiency, and minimizing costs. These models go beyond traditional strategies, integrating various factors such as demand variability, lead times, and service levels. Understanding these advanced concepts is crucial for companies looking to thrive in today’s fast-paced market environment.
Stochastic Inventory Models
Stochastic Inventory Models deal with uncertainty in demand. Unlike deterministic models, which assume that demand will be constant and known, stochastic models account for variability. This aspect makes them particularly valuable in industries where customer demand is unpredictable. The primary benefit of using stochastic models is their ability to provide a more realistic picture of potential inventory needs. By employing statistical distributions to model demand, these systems can offer insights that help in calibrating safety stock levels.
For instance, consider a fashion retailer that experiences fluctuating consumer demand based on seasons and trends. An effective stochastic inventory model can help that retailer adjust their inventory in real-time, ensuring they have enough product to meet customer whims without overstocking, which can tie up valuable capital.
Deterministic Models
On the other end of the spectrum, Deterministic Models operate under certainty. These models assume that future demand is predictable and can be calculated with accuracy. While they offer simplicity and ease of implementation, they can fall short in scenarios where demand is not steady. Businesses that face fixed order cycles and predictable demand patterns can benefit greatly from these models.
Economic Order Quantity (EOQ) is a well-known deterministic model, that finds the optimal order quantity a company should purchase. By balancing ordering costs with holding costs, it seeks to minimize total inventory costs. Still, companies should always remain vigilant as market conditions can change unexpectedly, potentially rendering these models less effective.
Continuous Review vs. Periodic Review
Choosing between Continuous Review and Periodic Review systems can significantly affect inventory management effectiveness. In Continuous Review, inventory levels are constantly monitored, and reorders are triggered immediately when stock drops below a predefined threshold. This proactive approach provides real-time responsiveness but requires sophisticated tracking systems.
Conversely, Periodic Review systems check stock levels at regular intervals. The downside is the potential for stockouts between reviews. However, this method can be more accessible for smaller operations that may not have the resources for continuous monitoring.
To summarize:
- Continuous Review
- Periodic Review
- Constant monitoring of inventory
- Immediate reorders when stock falls below a specific point
- Requires advanced tracking processes
- Stock levels checked at predefined times
- Reorders made based on observed levels
- Easier for smaller operations but risk of stockouts
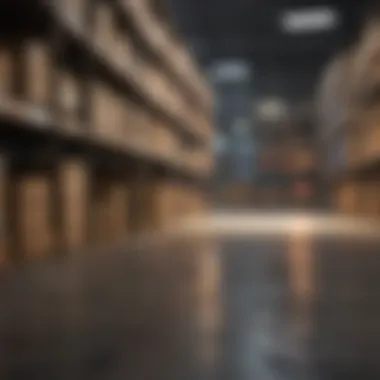
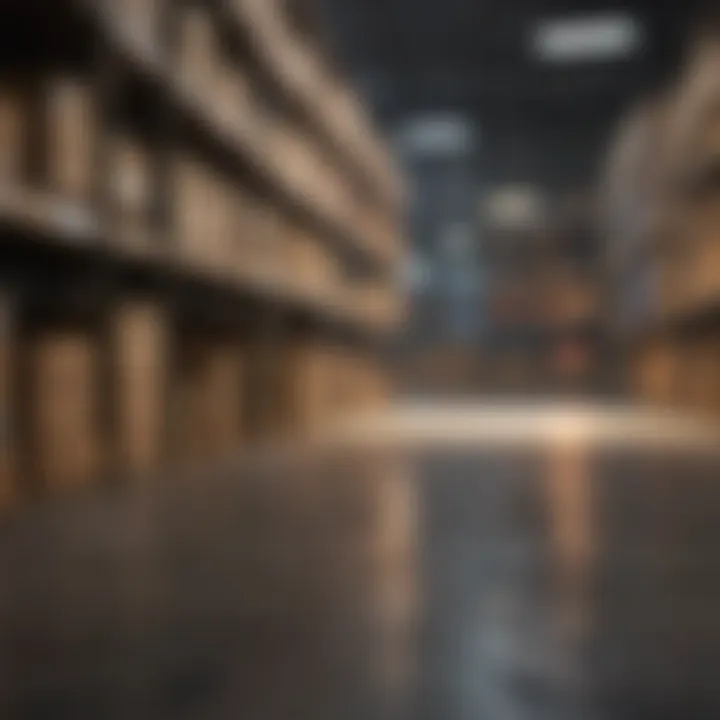
Both systems have their merits and should be selected based on specific business needs, inventory types, and customer expectations.
"Advanced Inventory Models are not just about technology; they are about understanding the intricacies of demand and supply dynamics to make informed decisions."
By integrating these advanced methods into supply chain strategies, companies can gain a competitive edge and ensure they are well-equipped to handle the demands of a dynamic market.
Demand Forecasting and its Role
Demand forecasting stands as a pivotal cornerstone in inventory management and supply chain efficiency. It involves predicting future customer demand for products or services, which directly impacts inventory levels, production schedules, and overall operational strategies. Accurate demand forecasting enables businesses to balance inventory costs, reduce excess stock, and mitigate stockouts, ensuring a more responsive supply chain.
In today's fast-paced market, the ability to forecast demand effectively is not just a luxury; it’s a necessity. Businesses face the challenge of adapting to fluctuating consumer preferences, seasonal trends, and competitive pressures. Therefore, implementing robust forecasting techniques leads to informed decision-making, optimizing inventory levels while also improving customer satisfaction.
Quantitative Methods
Time Series Analysis
Time Series Analysis is a statistical technique utilized to analyze data points collected or recorded at specific time intervals. This method is significant to supply chain inventory due to its ability to identify patterns or trends over time, making it a common choice in demand forecasting.
One of the key characteristics of Time Series Analysis is its emphasis on historical data. By examining past sales figures, companies can forecast future demand. This can be particularly beneficial in industries with relatively stable demand cycles, where historical patterns are less likely to deviate.
However, while this method has clear advantages—such as simplicity and a solid foundation on historical performance—it also comes with drawbacks. Unforeseen events or shifts in market dynamics can lead to inaccuracies, potentially skewing results if past conditions do not replicate.
Regression Models
Regression Models offer another valuable approach within quantitative forecasting. They evaluate the relationship between demand and one or more independent variables, allowing for a more nuanced prediction of demand.
The primary appeal of Regression Models lies in their versatility. They can incorporate multiple factors such as pricing, economic indicators, and market trends, making them applicable across various sectors. This key characteristic enhances their predictive accuracy, especially when conditions are no longer static.
However, the complexity of these models can pose challenges. They require rigorous data management and statistical expertise, which may not always be feasible for smaller businesses. Furthermore, overly relying on the model’s results without considering external variables can lead to misleading forecasts.
Qualitative Methods
Qualitative methods cast a different light on demand forecasting, focusing on insights and opinions rather than cold, hard data.
Expert Judgment
Expert Judgment relies on the insights of individuals with extensive experience in the industry. This method is particularly useful when historical data is scarce or unreliable. Key characteristics include a focus on qualitative insights, making it especially relevant for novel products or in rapidly changing markets.
The unique feature of Expert Judgment is its adaptability. It allows organizations to factor in the qualitative nuances of market trends, consumer behavior, and off-the-cuff insights that data alone may miss. Nonetheless, one must bear in mind that this method can be subjective and personalized; different experts may offer opposing views, leading to potential inconsistencies in forecast accuracy.
Focus Groups
Focus Groups leverage small groups of individuals to gauge perceptions and expectations about a product or market segment. This qualitative approach allows companies to tap into consumer sentiment and preferences, often providing deeper insights into potential demand curves.
The main draw of Focus Groups is their ability to unearth the motivations and opinions of consumers. This unique feature means businesses can better align their inventory to meet actual consumer needs, rather than relying solely on data-driven methods. However, the effectiveness can be limited by groupthink or dominant personalities skewing results, which may not represent the broader market.
"Accurate demand forecasting is akin to navigating a ship through stormy waters; it requires careful observation and adept handling to stay on course."
Finale
Incorporating both quantitative and qualitative methods, each with its strengths and weaknesses, can form a more holistic approach to demand forecasting in supply chain management. Understanding the significance of these methods creates opportunities for businesses to refine their inventory strategies, ultimately paving the way for enhanced operational efficiency and customer satisfaction.
The Impact of Technology on Inventory Models
In today's fast-paced business landscape, the impact of technology on inventory models is undeniable. Organizations worldwide are constantly seeking more efficient ways to manage and optimize their supply chains. The advancement of technology has not only simplified processes but also allowed for a level of accuracy and precision that was unattainable in the past. This section will delve into key technological innovations and their implications on inventory management, emphasizing how they drive efficiency and reduce operational costs.
Automation and Robotics
The role of automation and robotics in inventory management cannot be overstated. Businesses are increasingly adopting automated systems to streamline their operations. Here are several ways automation transforms inventory management:
- Efficiency Gains: Automated systems can handle tasks like inventory tracking, order fulfillment, and restocking with minimal human intervention. This reduces the time taken for these processes, allowing for quicker response times.
- Error Reduction: With machines taking over repetitive tasks, there is a significant drop in human error. This reduction leads to better inventory accuracy, ensuring that stock levels reflect what is physically available.
- Scalability: Automation provides companies the ability to scale operations effortlessly. When demand spikes, automated systems can handle increased workloads without compromising performance.
- Labor Cost Savings: While there is an initial investment in automated technology, the long-term savings on labor costs cannot be ignored. Businesses can allocate their human resources to more strategic roles rather than routine tasks.
However, the transition to automated systems is not without challenges. Organizations must invest in proper training for staff to work alongside these technologies. Moreover, initial setup costs can be substantial, which compels management to carefully weigh the cost-benefit ratio before implementation.
"Embracing automation isn’t just a trend; it’s a necessary step towards sustainable growth in inventory management."
Artificial Intelligence and Machine Learning
Integrating Artificial Intelligence (AI) and Machine Learning (ML) in inventory models heralds a new epoch in supply chain management. These technologies enable businesses to analyze vast amounts of data, leading to improved decision-making processes. The following points elaborate on their significance:
- Data-Driven Insights: AI and ML can sift through historical data to identify patterns and predict future outcomes. This capability enhances demand forecasting, allowing businesses to maintain optimal inventory levels, which in turn minimizes holding costs.
- Dynamic Decision Making: These technologies can provide real-time insights into inventory status, enabling organizations to respond promptly to any discrepancies, such as unexpected stockouts or overstocks.
- Customized Recommendations: Machine learning algorithms can analyze customer behavior and preferences, tailoring inventory to meet the specific needs of different market segments. This personalization can lead to increased customer satisfaction and sales.
- Risk Management: AI tools can also help predict potential supply chain disruptions. With advanced warning, companies can devise contingency plans to mitigate the impact on inventory management.
However, the adoption of AI and ML involves challenges such as data privacy concerns and the need for high-quality data inputs. Organizations must ensure they maintain the integrity and security of their data, as the value derived from these technologies highly depends on the quality of the information fed into them.
In summary, the advent of technology in inventory models serves as a game changer for supply chains. The effective implementation of automation and AI not only improves efficiency but also fosters a smarter, more responsive inventory management approach that aligns with contemporary business needs.
Sustainability in Supply Chain Management
Sustainability in supply chain management has become not just a phrase to bandy about, but a critical cornerstone for companies striving to maintain competitiveness while being responsible stewards of the environment. As businesses increasingly realize the long-term benefits of sustainable practices, the integration of eco-friendly principles into inventory management has a profound impact on efficiency and cost reduction. This section highlights the significance of sustainability, exploring how it can reshape inventory practices as well as overall supply chain strategies.
Eco-Friendly Inventory Practices
Adopting eco-friendly inventory practices is fundamental for companies aiming to lower their environmental footprints. It’s not just about a warm, fuzzy feeling; more and more consumers are choosing to do business with companies that display a commitment to sustainability. Here are some ways organizations can implement eco-friendly practices in their inventory management:
- Reduction of Waste: Streamlining processes to minimize excess stock not only cuts costs but also reduces potential waste. Consider a retailer switching to a just-in-time ordering system, managing to cut down on surplus inventory that may remain unsold.
- Sustainable Packaging: Many businesses are investing in biodegradable packing materials and recyclable containers. This choice can resonate positively with eco-conscious customers, improving brand loyalty.
- Energy Efficiency: Using energy-efficient technologies throughout the inventory process can lead to reduced energy consumption. For instance, upgrading to LED lighting in warehouses can produce significant savings over time while also reducing carbon emissions.
"Embracing sustainable practices is not merely a trend but a pathway towards longevity in a competitive market," states an industry analyst highlighting the necessity of sustainable strategies today.
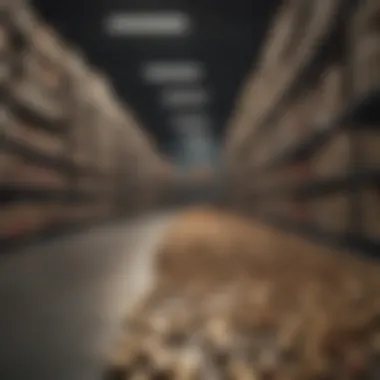
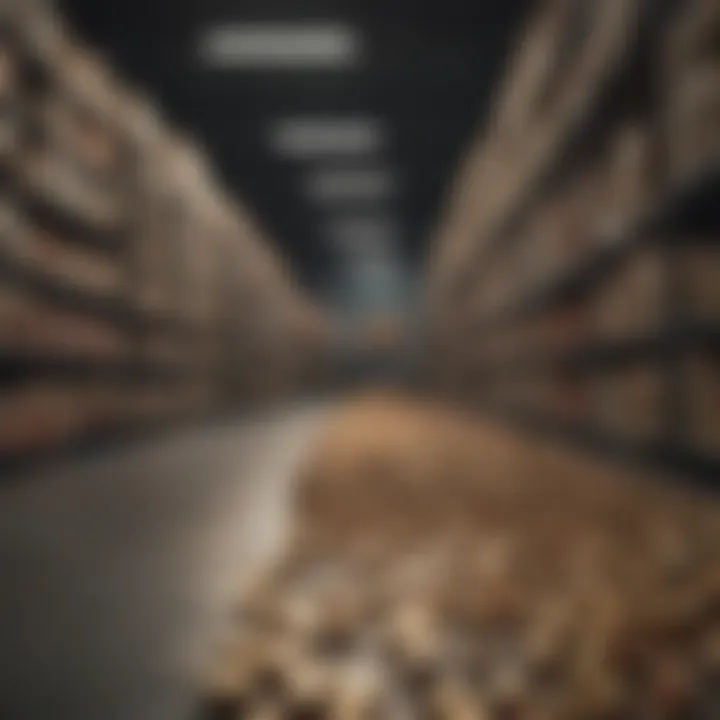
Incorporating these practices requires an upfront investment, but the long-term benefits often outweigh the costs.
Circular Supply Chains
The concept of circular supply chains shifts the traditional linear model—where resources are taken, used, and thrown away—into a cycle of renewal. It emphasizes reusing and recycling, and in doing so, it minimizes waste and promotes sustainability. Here are several key elements of a circular supply chain:
- Resource Recovery: Companies are rethinking how they can recover and reuse materials from their own production processes. For example, a manufacturer of electronics may set up programs to return old devices to extract reusable parts.
- Collaborative Consumption: Businesses can collaborate with each other by sharing resources, which helps reduce the overall consumption of materials. This approach promotes efficient usage and minimizes surplus.
- Design for Longevity: Products designed for durability and reparability can reduce the need for frequent replacements. Companies have seen success by focusing on producing items that last longer and can easily be repaired when needed.
The shift towards circular supply chains not only contributes to environmental sustainability but can also unlock new business opportunities by appealing to a growing base of environmentally-aware consumers. In today’s global marketplace, a sustainability focus is no longer an optional add-on; it’s essential for survival and success in the long run.
Challenges in Implementing Inventory Models
When delving into supply chain inventory models, recognizing the hurdles that businesses face is key. These challenges not only affect the efficiency of models but also their success in driving the intended results. Understanding these intricacies provides significant insight into why the smooth application of these models can often feel like navigating a minefield. Factors like data accuracy, technological disruptions, and organizational hurdles all contribute to the challenges in this area.
The significance of addressing these challenges is paramount in today’s fast-moving business landscape. Overcoming these obstacles can lead to enhanced operational efficiency, reduced costs, and a more agile inventory management system. To gain a competitive edge, businesses must pay attention to the following specific elements related to the challenges of implementing inventory models.
Data Accuracy and Quality
Data acts as the backbone of any inventory model. Without reliable data, any inventory strategy is like building a house on sand. Poor data quality can result in inaccurate demand forecasts, leading to either overstocking or stockouts. That's the kind of situation that can put a company’s bottom line at serious risk.
Here are some considerations regarding data accuracy:
- Data Integration: Various systems within an organization often work in silos. Ensuring that all data sources communicate effectively can significantly improve data quality.
- Real-time Updates: Inventory levels should be updated in real-time to reflect the latest information. Delays can disrupt the whole supply chain operation.
- Data Cleaning: Regular audits and cleans of the data set ensure that obsolete or incorrect data does not affect decision-making.
Implementing automated data checks can assist in maintaining this accuracy and quality, but initial investments often worry management. However, the long-term benefits outweigh these concerns.
Supply Chain Disruptions
In today’s unpredictable market, companies face various supply chain disruptions like natural disasters, political instability, and even a pandemic, as seen globally. These disruptions pose risks that can severely impact inventory availability and management. Adjustments to inventory models must be agile enough to adapt to these unforeseen events.
Some aspects to consider regarding supply chain disruptions include:
- Risk Assessments: Regularly perform assessments to identify weak points within the supply chain. This will help businesses anticipate and fortify against potential disruptions.
- Diversified Suppliers: Relying on a single supplier is a gamble. Diversifying the supplier base can spread the risk and ensure that if one supplier falters, others can pick up the slack.
- Flexibility in Models: Inventory models should be adaptable to shifting market conditions. For instance, during a supply chain issue, companies may need to adopt a safety stock policy.
Facilitating communication among stakeholders during disruptions can ease transitions. In essence, recognizing these challenges and creating strategic plans can streamline inventory operations and provide resilience against unexpected events.
"The best way to predict the future is to create it." – Peter Drucker
Case Studies of Successful Inventory Management
Case studies serve as a practical lens through which we can view theoretical concepts in action. Understanding how different businesses have effectively managed their inventory gives insight into the practical realities of various models and practices in the supply chain. They illustrate the challenges faced, solutions implemented, and the outcomes achieved, thus providing valuable lessons for professionals aiming to optimize their own inventory strategies.
By examining real-world examples, we gather evidence on how specific inventory management systems, like Just-In-Time, can dramatically affect the operational efficiency of a company. Such studies allow us to identify common challenges, innovative solutions, and the critical factors that contribute to successful inventory management. This exploration not only solidifies our understanding of advanced methodologies but also encourages the adoption of best practices across various businesses.
Case Study: Toyota and JIT
Toyota is often heralded as the flagship example of Just-In-Time (JIT) inventory management. The company revolutionized the automotive industry with its innovative approach. At the heart of JIT is the principle of minimizing waste. By reducing the amount of inventory on hand, Toyota not only cut costs but also improved production efficiency. An insightful aspect of Toyota's strategy is its focus on building strong relationships with suppliers. This allows them to receive materials only as needed, aligning supply closely with production schedules.
The company employs Kanban, a visual scheduling system, to trigger ordering processes. By utilizing Kanban, Toyota monitors production levels effectively and avoids unnecessary stockpiling. Implementing this model has enabled Toyota to respond quickly to market changes while maintaining high quality standards. The trade-off? The risk of supply chain disruptions is heightened. However, Toyota's meticulous planning and robust supplier relationships have been pivotal in mitigating this risk.
"By emphasizing lean production and JIT, Toyota not only transformed its manufacturing processes but also set a benchmark in supply chain efficiency."
From this case, several key takeaways emerge:
- Supplier Collaboration: Building strong, reliable relationships with suppliers.
- Waste Minimization: Reducing excess inventory leads to cost savings and improved cash flow.
- Responsiveness: The ability to quickly adapt production levels to fluctuating demand is essential.
Case Study: Amazon and Technology Integration
Amazon has continuously pushed the envelope when it comes to leveraging technology for inventory management. The company’s use of sophisticated algorithms and data analytics allows for precise demand forecasting, meaning it can maintain optimal stock levels without overinvesting. By analyzing purchasing history and current market trends, Amazon accurately predicts what products will need restocking and when.
A key feature of Amazon’s inventory model is its use of automation in warehouses. Robots are employed to transport goods, minimizing the time human workers spend on repetitive tasks and maximizing efficiency. This not only speeds up order fulfillment but also decreases errors in the logistics process.
Additionally, Amazon’s Prime subscription service, which promises rapid delivery times, relies heavily on its inventory being in the right place at the right time. By using predictive analytics, Amazon enhances its supply chain agility, reducing potential stockouts and improving customer satisfaction.
In summary, the success of Amazon demonstrates how technology can integrate seamlessly with inventory management practices to achieve substantial results:
- Data-Driven Decisions: Leveraging analytics for informed stock management.
- Automation: Increasing efficiency through robotics.
- Customer-Centric Focus: Meeting customer demand accurately and swiftly.
By dissecting these case studies, we can glean essential techniques and strategies that are instrumental in modern inventory management. The experiences of both Toyota and Amazon not only highlight effective practices but also the importance of adaptability in dynamic market environments.
Future Trends in Supply Chain Inventory Models
In the fast-evolving world of supply chain management, adhering to traditional methodologies can leave businesses trailing behind. As market demands intensify and technological advancements accelerate, it’s crucial to keep an eye on future trends that are carving new paths for inventory models. By understanding these trends, businesses can not only optimize their current practices but also position themselves ahead of potential challenges.
Blockchain Technology
Blockchain technology, often synonymous with cryptocurrency, is expanding its reach into supply chain inventory management. This technology ensures transparency and security in transactions, making it easier to track goods throughout the entire supply chain. Businesses can leverage blockchain for real-time data access, fostering trust among partners and customers.
Key Benefits of Blockchain in Inventory Management:
- Enhanced Traceability: Each transaction is recorded in a way that allows all parties to see the entire history of the product, thus minimizing disputes.
- Improved Efficiency: By automating and streamlining processes, blockchain reduces the need for manual checks and balances, leading to significant time savings.
- Cost Reductions: Minimizing errors can lead to financial savings, reducing unnecessary expenditure on resolutions.
"With blockchain, we can anticipate the unexpected. It's not just about storing records, it's about building a more resilient supply chain."
Implementing blockchain, however, isn’t a walk in the park. Companies must invest in the necessary infrastructure and training to adopt this technology effectively. Additionally, there is a need for standardization among industries to fully reap the benefits of blockchain.
Predictive Analytics
Predictive analytics stands as another game-changer for supply chain inventory models. By utilizing historical data and advanced statistical algorithms, businesses can forecast future inventory needs with increased accuracy. This is crucial as it allows for better decision-making regarding stock levels, purchasing, and resource allocation.
Benefits of Predictive Analytics in Inventory Management:
- Demand Anticipation: Companies can foresee market fluctuations and adjust their inventory accordingly, thus avoiding stockouts or excess capacity.
- Strategic Planning: Supply chain leaders gain insights that help in planning logistics, labor requirements, and financial forecasting more effectively.
- Enhanced Customer Satisfaction: With the right inventory at the right time, customer needs can be met without delay, boosting brand loyalty.
The introduction of predictive analytics requires investment in data collection and analytical tools. However, the payoff can be substantial, offering companies a clearer view into their operational needs.